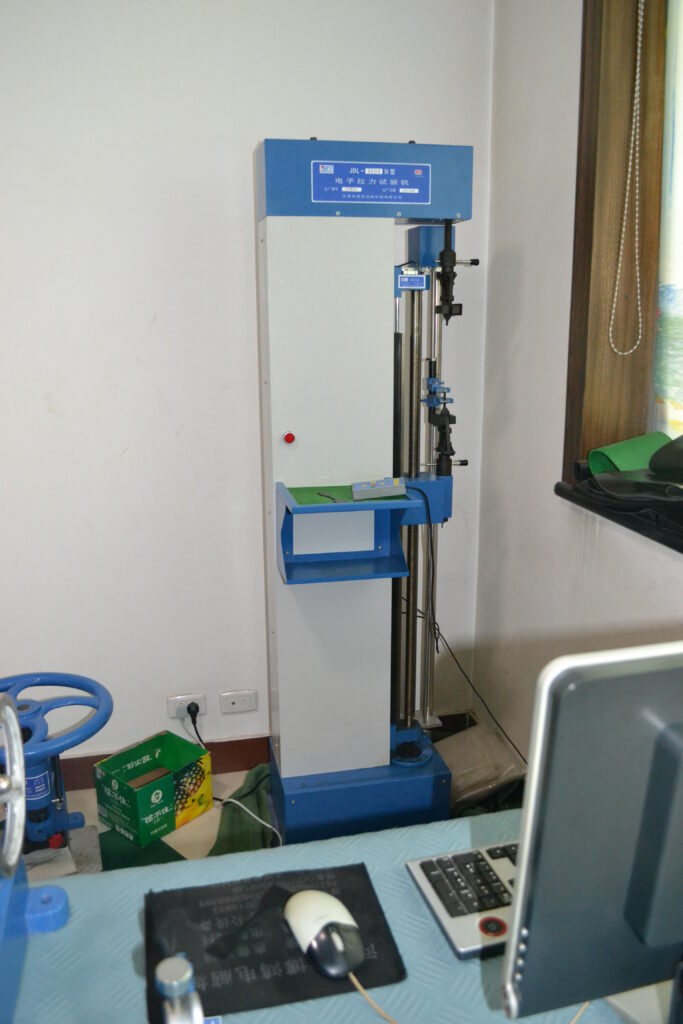
Because of the market demand, more and more manufacturers of industrial rubber plate are now produced. Today’s content is about the Factors affecting tensile strength of industrial insulating rubber sheet, let’s take a look at it together!
First, In formulation design, type and content of raw rubber, vulcanization system and filler is the mainly factor affecting tensile strength of industrial insulating rubber sheet. The formula with high tensile strength shall be made of crystalline rubber such as natural rubber, neoprene rubber or chlorosulfonated polyethylene, with the rubber content generally about 60%.
Second, the active fillers (such as carbon black and white carbon black) should be selected and dispersed evenly during mixing. When using active packing, the dosage should be suitable.
Third, the tensile strength is related to the structure of rubber, and the sub valence health of molecular interaction is smaller when the amount of the rubber is small. All other factors that affect the inter molecular forces have an effect on tensile strength
Fourth, tensile strength is also related to the root temperature, and the tensile strength at high temperature is far lower than that at room temperature. The tensile strength of the root is related to the crosslinking density. With the increase of the crosslinking density, the tensile strength increases. After the maximum value, the crosslinking density will continue to increase, and the tensile strength will decrease greatly.